The Coming of Age of Lyophilization
- vincenzo esposito
- Jan 16, 2019
- 3 min read
Updated: Jul 23, 2020
Many biotechnologically manufactured substances are not sufficiently stable in aqueous solutions. Because of this, liquid formulations are quite difficult or in some cases, merely impossible to preserve for longer periods. One solution, however, is freeze-drying, by which water is extracted from the substance in solution under vacuum and low temperatures. Still, before being administered to the patient, the drugs must be reconstituted. The freeze-drying offers drug manufacturers a range of options for packaging, such as sterile WFI syringes and dual chamber systems.
With the growth of the biologics market, four of the world’s top-five selling drugs are delivered by injection. Because these drugs are complex, biologics often require robust design efforts and present delivery challenges.
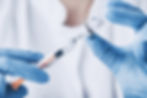
The Right Packaging
Companies that manufacture freeze-dried substances have a range of packaging solutions on the market from which to choose. In addition, each system has its own processing requirements, offering its own set of possibilities for efficiency. These options include:
Vials
Dual-chamber syringes
Dual-chamber cartridges
Vials
The industry standard for freeze-drying products is the vial. The majority of pharmaceutical and biotech companies with a freeze-dried product initially develop in vials. The main reasons for this are the development process and the regulatory requirements are generally well known. Development in a vial is a less-complex process and this can reduce the overall risks in clinical phases. Because of these factors, time-to-market can be reduced in turn increasing the length of patent protection.
However, only experienced users should use vials with freeze-dried substances due to the fact that reconstitution requires several steps.
Dual-Chamber Syringes
Dual-chamber syringes are one of the more innovative packaging forms for freeze-dried substances and are particularly good for single doses and filling volumes ranging from 0.1 ml to 5 ml. This “all-in-one” option places the freeze-dried substance and the solvent in the same system. Their assembly, however, is a lot more complex than vials, consisting of a glass body separated into two chambers by a central stopper. Additionally, an end-stopper, plunger, and a closure are also needed. The syringe body and components must also be siliconized in order to obtain suitable break loose and glide forces. Due to the smaller diameter, the geometry of the frozen matrix during drying offers more resistance, which can result in longer drying times.
Dual-Chamber Cartridges
Dual-chamber cartridges are yet another development of dual-chamber syringes, providing fill volumes of 0.1 ml to max 1 ml for single and multiple doses. They have both the advantages and disadvantages of dual-chamber syringes as it pertains to structure. The closure is different, however, and consists of an injection membrane for needles. The dual-chamber cartridge is ideal for use in pen systems and simple drug delivery. There are special cartridge closures available that can be sealed in the lyophilizer, thus creating a nitrogen atmosphere over the product, which helps maintain the low residual moisture. Final assembly of the system also requires careful calibration with the pen system.
Future Drug Devices
No matter the type of packaging, in the future drugs will have to be practical and fits into device/injectors with the following characteristics:
Universal: They will operate with any primary container without the need for a drug transfer step.
Customizable: Embedded electronic features will allow customization depending on the intended user type.
Upgradable: Connectivity capabilities will allow devices to be remotely upgraded, making the task of lifecycle management easier.
Green: Devices will further align with the increased requirement for greener technologies.
Empowering: Injectors will allow patients to take control of their disease state by monitoring their drug performance and recording relevant everyday activities. Access to real-time and historical data will empower patients who want the ability to better manage their disease state.
Trying to predict future developments in freeze-drying represents a major challenge, although PAT tools and new freeze-drying methods (such as continuous freeze-drying) will definitively focus on energy consumption and the growing need for flexibility (fewer "block buster" products and "personalized medicine" are likely to have a significant impact in the manufacturer industry).